Capabilities
Facilities Overview
- Over 22,000 sq ft facility with additional space available for manufacturing and R&D suites
- Over 9 ISO 7 or ISO 8 certified clean room suites & 2 non-classified Manufacturing suites
- 2 suites are dedicated for toxic product manufacturing, 1 new suite added for Potent Products.
- Manufacturing Capability from grams to 100kg batch size for specialty products.
- Flow & continuous manufacturing batch sizes can be larger based on process parameters.
- QC laboratory ~1,000 sq ft equipped with all frequently used instruments
- Power Backup generator
- Water-for-injection specification water manufactured on-site since 2009 (system replaced in 2023 with higher capacity)
- FDA Registered Establishment – 3007640515
- DEA Schedule II to V Researcher Registration – RS0683359
- Compliant as federal large generator of hazardous waste with EPA registration – MOD174885905
Manufacturing Capabilities
Focused on Complex Pharmaceutical Molecules (Small molecules), High Potency molecules, DEA schedule II to V molecules and Toxic Substances in highly contained environment.
Chemical Synthesis | Filtrations | Drying |
Glass Reactors Stainless Steel reactors High Temperature High Pressure reactors Vacuum Distillation Centrifuging and separation | Ultrafiltration / Diafiltration (UF/DF) Microfiltration (Bioburden and endotoxin control) | Vacuum Cone Dryer Rotary Evaporator Convection Oven |
Potent & Toxic Substance Handling | Utilities | Reaction Capabilities |
Dedicated Suite Solid powder and Vapor containment Employee Protection and Environmental Monitoring for Contamination Single use disposal technology Exhaustive end-of-campaign cleaning process Validated equipment cleaning process | Chiller Vacuum Compressed Air Nitrogen Water for Injection (WFI) | Batch processes (Coupling, Substitutions, Oxidation, Reduction, Sulfonation, etc) Continuous liquid-liquid reaction process High temperature high pressure processes Natural Product extraction and purification processes Natural Product based API Regulatory approval process know-how |
Continuous Manufacturing, Flow Chemistry, Automation, Batch Manufacturing, Any Other New Technologies | ||
Comprehensive services for scaling up flow chemistry processes from laboratory to commercial-scale cGMP production using Quality by Design and Q13 compliance. Our capabilities include: |
Analytical Capabilities
On-Site Capabilities | |
• HPLC (RI and UV detectors) • Ion Chromatography • UV Spectrophotometer • KF Titrator • Endotoxin Test Kit • pH / Conductivity/Brix meters • Polarimeter • NMR (Bench-top) | • Colorimeter • FT-IR Spectrometer • Titration • Wet and Dry chemistry • Dissolution • Bioburden • Total Organic Carbon |
Outsourced Capabilities | |
• LCP-MS • LCP-OES • NMR • GC • LC-MS | • Sterility • Product Bioburden • PolyMorph Solid STATE Form • Crystallinity – XRPD • Particle Size |
Quality
Sentio is registered with the FDA under FEI registration 3007640515
Our quality system is designed to comply with the requirement of FDA regulations 21 CFR Parts 210, 211, 820, Part 11, ICH Q7, ICH Q13, and relevant ICH guidelines for API and Drug Products.
Sentio has been inspected every 2 years by FDA since 2015 and has remained compliant and in good standing.
- Over 200+ Active Standard Operating Procedures (SOPS)
- Over 164 Active Specifications & Test Procedures
- Over 15 Product Master Manufacturing Records
- Comprehensive OJT & on-going training
- Schedule & work orders for preventive maintenance & calibrations
- Suppliers & Materials qualified
- Production & Laboratory equipment qualified & process/methods validated
- Reconciliation & secure storage of labeling
- final product stored within appropriate temperature & Humidity
- On-going stability program in-place
- Robust Quality management system in place

Innovation | Collaboration | Commercialization
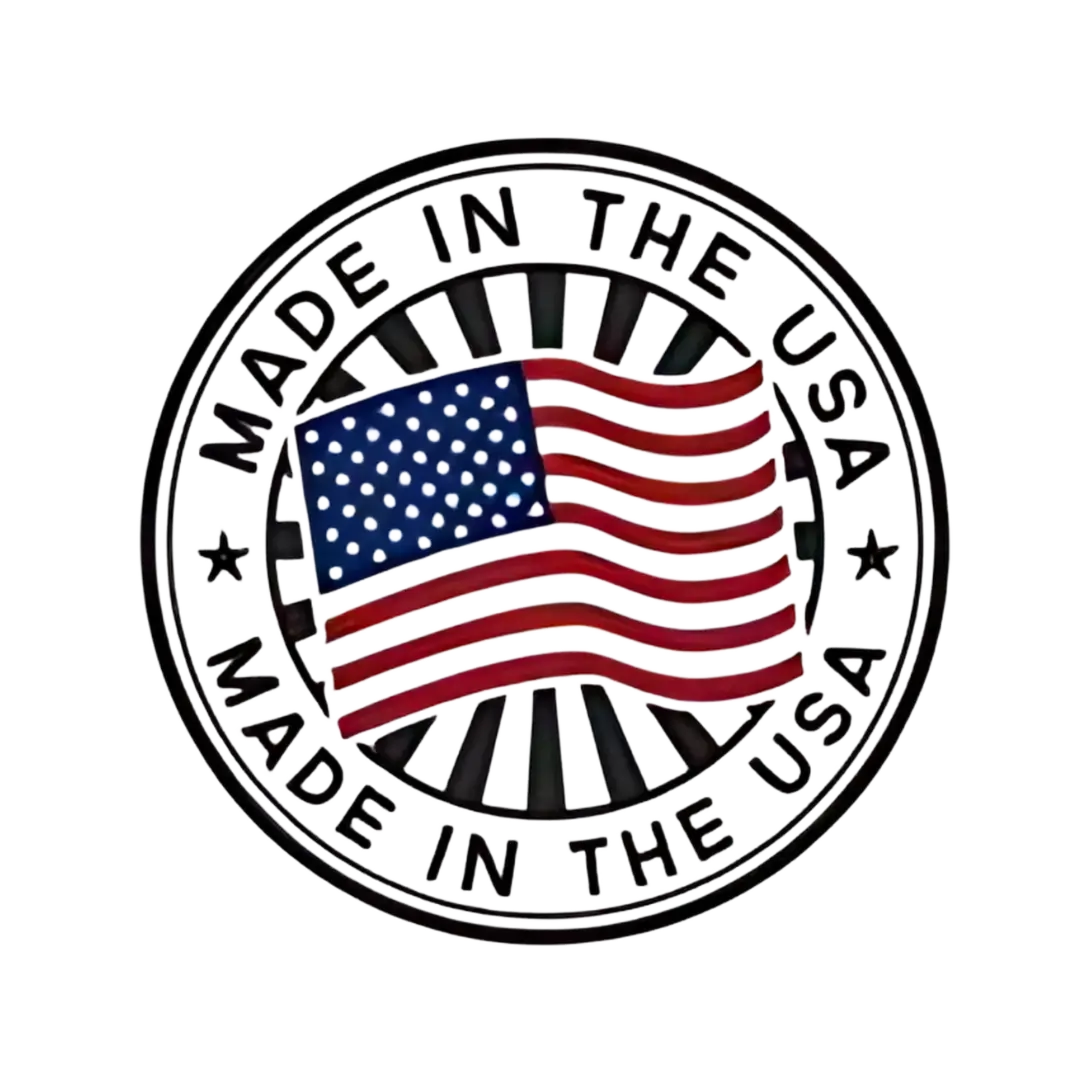
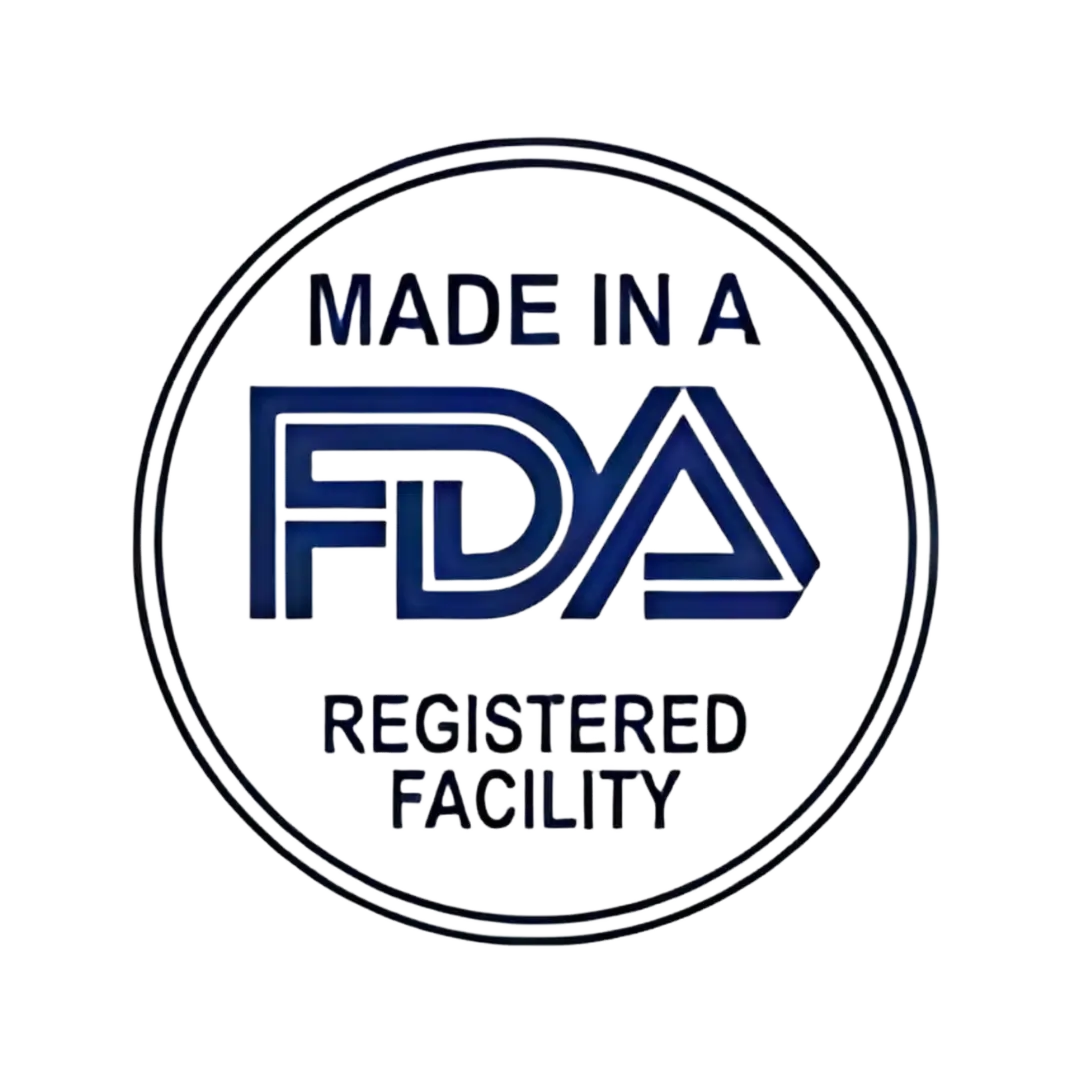
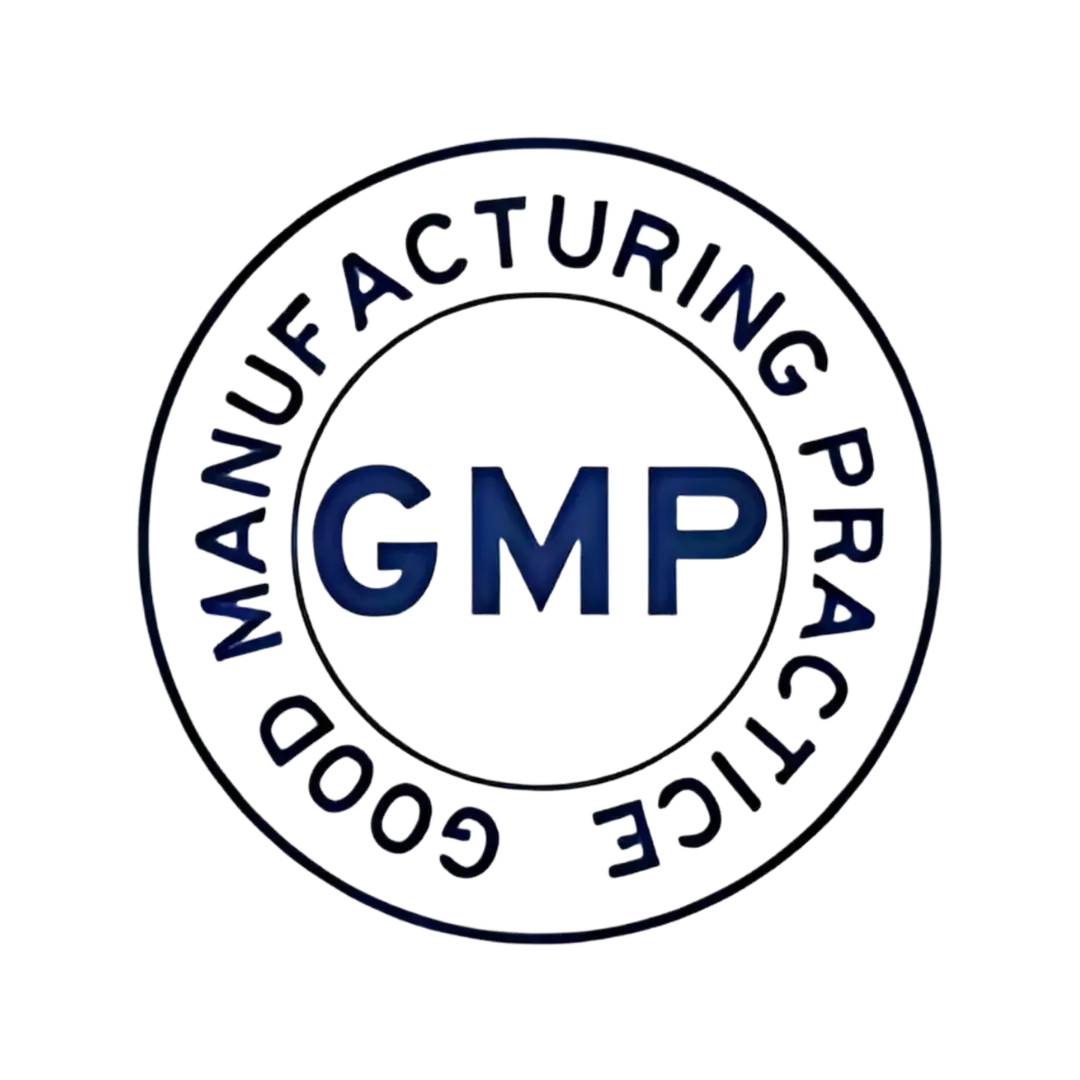
